Digital twins for building owners are emerging tools for facilities management, operations, and maintenance. The benefits of digital twins to overall businesses beyond traditional practice are just beginning to be realized. This article provides background information on digital twins as a starting point for the AU 2020 roundtable and AU 2021 panel discussions exploring what digital twins mean for the building industry today.
Digital twin strategies started in the digital manufacturing, product, and machine industries. This practice was spearheaded as far back as 2016 by companies such as GE and Siemens. Digital twins are currently defined as software representations of assets, and processes that are used to understand, predict, and optimize performance in order to achieve improved business outcomes.
Related: Extending the Value of BIM to Owners with a Digital Twin with Robert Bray
Digital twins consist of three components: a data model, a set of analytics or algorithms, and knowledge. Digital twin practices leverage data tactics from other trending technologies like AI-driven development (artificial intelligence), predictive/augmented analytics, IoT (Internet of Things), and IIoT (Industrial Internet of Things) to enhance next-generation PLM (Product Lifecycle Management) and PDM (Product Data Management). For the building industry, it is an emerging technology and set of practices still being defined and understood.
Like most trending industry technology terms such as '3D printing' and 'mixed reality,' the term 'digital twin' is overused and misinterpreted in the AEC industry. Most commonly the use confuses record drawings and models with a digital twin. The hype versus reality couldn’t be more apparent in today’s building industry vernacular. The industry buzz around digital twin hit its plateau in 2018-19, according to Gartner. The term is not even mentioned in any public Gartner Hype Cycles for 2020-21. If digital twin is really moving from the Trough of Disillusionment and into the Slope of Enlightenment, then a more balanced, rational, and practical understanding of the concept will eventually emerge.
Owner's Dilemma
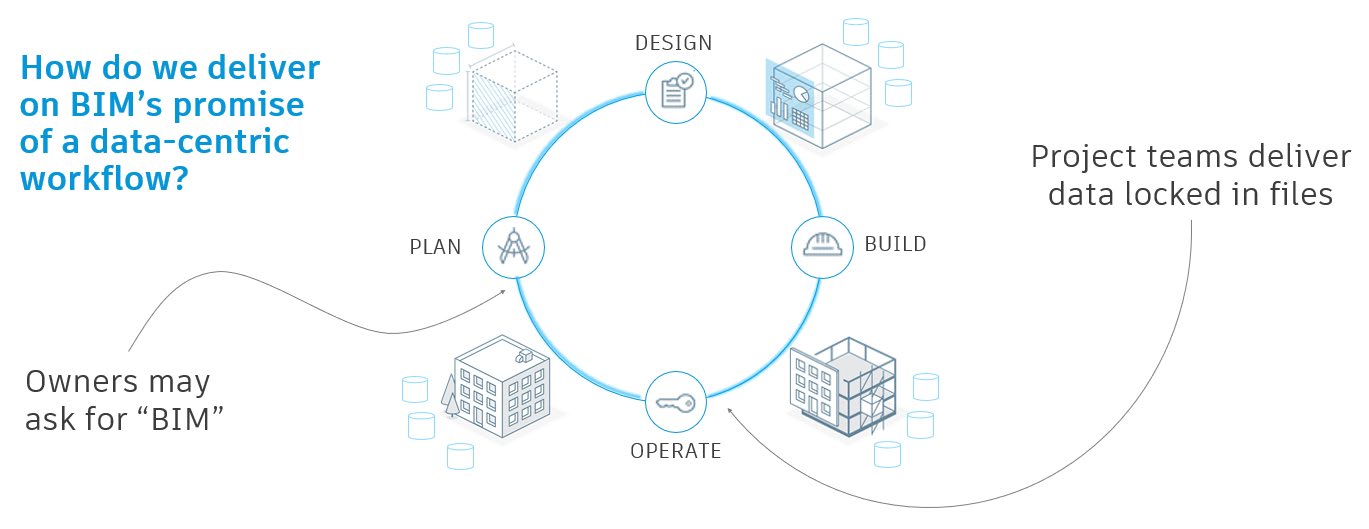
Building owners and operators ("owners") have long understood the need for both geometric model representation and associated metadata of building systems for operational and maintenance needs. Owners struggle in obtaining both complete and accurate building data. The traditional practice of obtaining record, as-builts, as-constructed drawings is a flawed and inefficient practice in providing the level of detail and accuracy required. Managing as-constructed and as-designed conditions from contractors, trades, and design consultants is also an inefficient workflow during the construction phases.
From a professional fee perspective, it’s poorly planned as a deliverable and resources requirement. BIM practices have helped with providing models and data deliverables, but owners still struggle with platform integration and metadata standards to make the requirement efficient, repeatable, and scalable.
Facility management practices of maintaining key data like manuals and asset warranties for building management systems can be inaccurate due to a lack of industry data standards and common platforms. Real-time operational data needs with digital monitoring and sensors are currently explored but systems are costly and business value ROI does not make it affordable yet. Owners that have BIM data requirements typically don’t have the resources and time required to validate compliance of deliverables.
Handover from designers, engineers, and contractors to the owner at substantial completion is still a traditional practice of 2D PDF deliverables in most cases. FM/PLMs are large databases but only digital records of known conditions of the building(s). This information requires continuous human intervention to validate, maintain, and update. Currently most FM/PLM systems have only basic automated maintenance scheduling, asset tracking, and management features. They require high levels of customization to meet owner needs and are relatively expensive to operate and maintain. This type of digital record keeping is not digital twin.
Owners also struggle with building renewal and renovation cycles. Property management, forecasting development, space planning, and programming requirements of existing assets to new or repurposed uses need improvement in data understanding.
What is the value of the digital twin to owners? It is a highly accurate and complete digital single point of truth of the build conditions and that information is always kept current and activities are regulated and visible. Operation and maintenance are proactive and automated based on data gathered during daily operations. Digital twin also aids better understanding in building renovation and renewal.
Digital twin doesn’t need to start at building commissioning. Design models are digital prototypes for the building(s). The evidence of collected data over time can be used to inform design decisions. The collection and understanding of design and business decisions over time allows for enhanced knowledge and understanding of buildings, knowing not only the 'what' in a building, but also the 'why' of it.
Key Concepts
From the Gartner report of Top 10 Strategic Technology trends for 2019:
A digital twin is a digital representation that mirrors a real-life object, process, or system. Digital twins can also be linked to create twins of larger systems, such as a power plant or city. The idea of a digital twin is not new. It goes back to computer-aided design representations of things or online profiles of customers, but today’s digital twins are different in four ways:
1. The robustness of the models, with a focus on how they support specific business outcomes
2. The link to the real world, potentially in real time for monitoring and control
3. The application of advanced big data analytics and AI to drive new business opportunities
4. The ability to interact with them and evaluate “what if” scenarios
The focus today is on digital twins in IoT, which could improve enterprise decision making by providing information on maintenance and reliability, insight into how a product could perform more effectively, data about new products, and increased efficiency. Digital twins of an organization are emerging to create models of organizational process to enable real-time monitoring and drive improved process efficiencies.
Brandon Wlosinski works as the BIM technical specialist with the WDW Facility Asset Management teams. Brandon works with interdisciplinary teams of many sizes, within and outside, providing support and leadership for process and deliverables, centered around models and data. He also works to help set, maintain, and enforce company standards so that data and documentation can be made readily available for partners within The Walt Disney Company. He also works to build up tools and workflows for better safety and efficiencies of the project team. This includes areas such as VR/AR, IoT, building analytics, agile construction, and computational design.
Dorian Chau orchestrates design technology solutions for major global organizations and is a principal business consultant at Autodesk. He combines his background in architecture and expertise in design technology to help organizations transform their business by optimizing workflows through innovation and enables new capabilities in the design, build, and manage lifecycle including tech giant campuses and top tier resorts. He also brings his deep foundational understanding of design technology, digital transformation, and BIM to the engineering and manufacturing spaces. Prior to joining Autodesk, Dorian was the firm-wide BIM manager at Gensler, where he managed and refined the firm’s BIM strategy for seven years.